Almi
30,000 m² spice production: A challenge for process control technology.
The innovative system planning of the production site and the company headquarters led to a tripling of production.
The entire process is controlled via high-performance networked SIMATIC S7 control systems, which receive the order data and process parameters from the higher-level ESAweight process control system and provide actual data directly to the process control system for booking, logging and optimization.
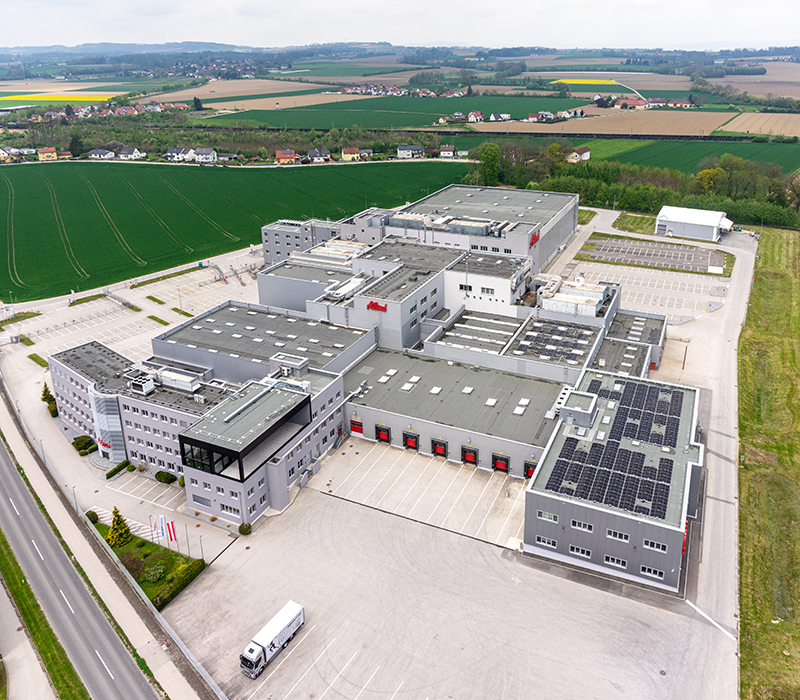
First priority in processing: Preserving the aroma!
Almi uses the extremely gentle cold grinding process to ensure that the raw materials are processed intact. During the grinding process, the raw materials are cooled using nitrogen. All data required for these important process steps can be freely defined in a so-called grinding recipe and are processed fully automatically by powerful PLC controls. All grinding workstations are equipped with a touch screen and corresponding ESAmill operating module for comprehensive and convenient operation.
Key position in the company: Container logistics for 70 containers in parallel
Up to 70 containers are transported on roller conveyors throughout the facility. Each one is assigned to an order. Depending on the order, the individual container collects the automatically pre-dosed individual components from a total of 40 raw material silos. Using a fully automatic crane system, the respective container is positioned over the mixing lines, docked and emptied, residue-free, by a container emptying system. Cameras are used to check the containers for residues. The ESAweight process control system takes care of the entire logistics of the containers on their way through production, with the manipulations being processed with high precision and absolutely error-free.
Requirements for Process Automation
- 80 dosing stations
- 40 automatic scales
- 30 manual dosing stations
- 15 mixing stations
- 5 grinder workstations
The new production system is considered a best practice example not only in terms of performance, but also in terms of flexibility.
Customer-specific orders can be produced and delivered at very short notice, and recipe changes or additional orders can be implemented in production within a very short time.
The ESAweight production control system currently installed on several servers and over 80 dosing stations provides a solid foundation for this.
Modules at Almi.
„
The container system enables flexible production with maximum efficiency, which is crucial when there are so many different customer-specific recipes or orders. In systems with fixed containers, the entire line must be cleaned after each order, resulting in downtime. Using our approach, however, the system remains in constant operation due to the high number of containers available, significantly increasing the utilization rate.
Robert Leeb | Almi, Head of Technical Department